
ANCHOR BRONZE
& Metals, Inc.
Quality & Deliveries You Can Trust

MADE IN THE USA
CONTINUOUS CAST BRONZE
C90300 (SAE 620) NAVY G Tin Bronze is a high wear resistant bronze that provides good mechanical properties and excellent corrosion resistance to dezincification. This proven alloy is used in wide applications and has an excellent rating for soldering and offers good brazing. Conforms to continuous cast specification ASTM B505
Chemistry: Cu88 Sn8 Zn4
Min. Mechanical Properties: 45 ksi tensile, 21 ksi yield (0.5% Ext. under load), 30% elongation in 2 inches, 70 Brinell Hardness (500 kg load)
Applications: Bearings, bushings, piston rings, valve components, seal rings, steam fittings and gears
C90500 (SAE 62) Tin Bronze also known as Gun Metal is a high wear resistant bronze that provides good mechanical properties and excellent corrosion resistance to dezincification. This proven alloy is used in wide applications and has an excellent rating for soldering and offers good brazing. Conforms to continuous cast specification ASTM B505
Chemistry: Cu88 Sn10 Zn2
Min. Mechanical Properties: 45 ksi tensile, 22 ksi yield (0.5% Ext. under load), 25% elongation in 2 inches, 75 Brinell Hardness (500 kg load)
Applications: Marine pumps, valves, bearings, bushings, piston rings, steam fittings, and gears.
C90700 (SAE 65) Tin Bronze is primarily a gear bronze. It is strengthened by the solid solution of tin in the copper. This results in a strong, hard intercrystalline phase rich in tin. The tin atoms distort the copper matrix enough to help inhibit slip of crystal layers and the intercrystalline phase contributes to hardness. The tin bronzes do develop a low friction deposit of bronze on the mating steel parts. For this reason, tin bronze is the alloy of choice for nonferrous gears. Conforms to continuous cast specification ASTM B505
Chemistry: Cu89 Sn11
Min. Mechanical Properties: 38 ksi tensile, 25 ksi yield (0.5% Ext. under load), 18% elongation in 2 inches, 65 Brinell Hardness (500 kg load)
Applications: Heavy duty gears, high load bearings, bushings and worm wheels.
C92200 (SAE 622) Navy M Tin Bronze is a high-grade steam-metal or valve-bronze alloy used for component castings of valves, flanges, and fittings. This alloy can be used for a variety of steam pressure applications involving temperatures up to 550F. Conforms to continuous cast specification ASTM B505
Chemistry: Cu88 Sn6 Zn4 Pb2
Min. Mechanical Properties: 38 ksi tensile, 25 ksi yield (0.5% Ext. under load), 18% elongation in 2 inches, 65 Brinell Hardness (500 kg load)
Applications: Valves, fittings, Medium-pressure hydraulic and steam pressure parts for use up to 550 F (287 C)
C93200 (SAE 660) Bearing Bronze has excellent load capacity and antifriction qualities that make it a preferred alloy for a wide variety of applications such as machine tools, power transmission equipment, electric motors, automotive equipment, tractors, cranes, hoists, elevators and many types of accessory and special equipment. C93200 bearing bronze has good machining characteristics, resists many chemicals and is generally recommended for medium speed, medium load applications. Conforms to continuous cast specification ASTM B 505.
Chemistry: Cu83 Sn7 Zn3 Pb7
Min. Mechanical Properties: 35 ksi tensile, 20 ksi yield (0.5% Ext. under load), 10% elongation in 2 inches, 65 Brinell Hardness (500 kg load)
Applications: General utility bearings, bushings and wear plates for medium speeds and pressures.
C95400 Aluminum Bronze is the most popular, all-purpose aluminum bronze alloy. It provides high yield and tensile strength, good ductility, weldability and exceptional resistance to wear, fatigue and deformation under shock or overload. C95400 aluminum bronze is recommended for high load, high wear applications. Conforms to continuous cast specification ASTM B 505
Chemistry: Cu87 AI10 Fe3
Min. Mechanical Properties: 85 ksi tensile, 32 ksi yield (0.5% Ext. under load), 10% elongation in 2 inches, 170 Brinell Hardness (3000 kg load)
Applications: High strength bearings, bushings, gears, worms, wear plates, valve seats, and guides.
C95500 Nickel Aluminum Bronze is recommended for heavy-duty applications involving abrasion, wear, and fatigue. The alloy exhibits exceptional yield, compressive strength, high hardness, and fairly high elongation. The addition of nickel offers superior saltwater corrosion resistance. Conforms to continuous cast specification ASTM B505
Chemistry: Cu81 AI10 Ni5 Fe4
Min. Mechanical Properties: 95 ksi tensile, 42 ksi yield (0.5% Ext. under load), 10% elongation in 2 inches, 190 Brinell Hardness (3000 kg load)
Applications: High strength bearings, corrosion resistant parts, aircraft valve guides, and seats.
C95510 HT (AMS 4880) Nickel Aluminum Bronze is one of the more popular landing gear bushing materials specified today along with C63000 material. The continuous cast alloy is heat treated and exhibits high mechanical strength which meets the properties of C63000 (AMS 4640). The alloy can be used as a substitute for C63000 in many applications. C95510HT (AMS 4880) is available in tube form, which requires less machine time and results in cost savings.
Chemistry: Cu78 min Al10 Ni5 Fe3 Mn 1.5
Min. Mechanical Properties: 105 ksi tensile, 62.5 yield, 9% elongation in 4D, 192 Brinell Hardness (3000 kg load)
Applications: Landing Gear Bushings & Bearings, Valve Guides, Stems, Seats, Corrosion Resistant Parts, Wear Rings, Machine Tool Parts, Piston Guides, Worm Wheels, Propeller Hubs, Wear Rings, Hardware, Worm Gears, Shafts, Sleeves
C86300 (SAE 430B/ALLOY 424) Manganese Bronze is a high strength, non-heat treatable alloy intended for use in applications requiring a good combination of outstanding wear characteristics and high bearing strength. C86300 SAE 430B manganese bronze is recommended for low speed, extreme load applications. Conforms to continuous cast specification ASTM B 505
Chemistry: Cu63 Al6 Fe3 Mn3 Zn25
Min. Mechanical Properties: 110 ksi tensile, 62 ksi yield (0.5% Ext. under load), 14% elongation in 2 inches, 225 Brinell Hardness (3000 kg load)
Applications: Heavy duty high strength alloy for gears, cams, slow speed heavy load bearings, screw down nuts.
Other Cast Copper Alloys are available in a wide variety of sizes from 0.406" (10.30mm) diameter up to 16.00" (406mm) diameter or cross-section and are available in tubes, solid diameters, rectangles, squares, hexagons and special profiles. Bar lengths are available in 144" standard mill lengths or cut to your requested length. Centrifugal Cast (ASTM B271) rings and tubes are available up to 124" (3150mm) outside diameter.
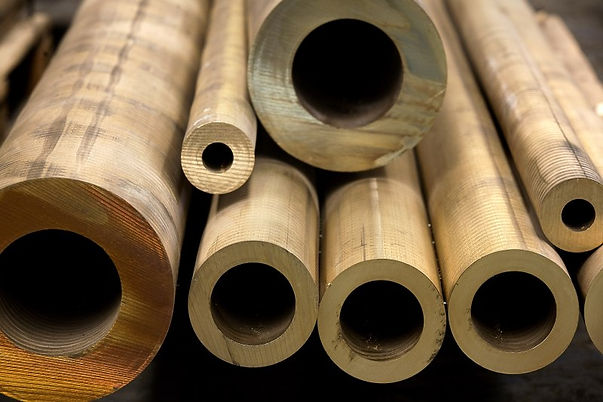
